Qué es el Mantenimiento Correctivo: Guía Práctica
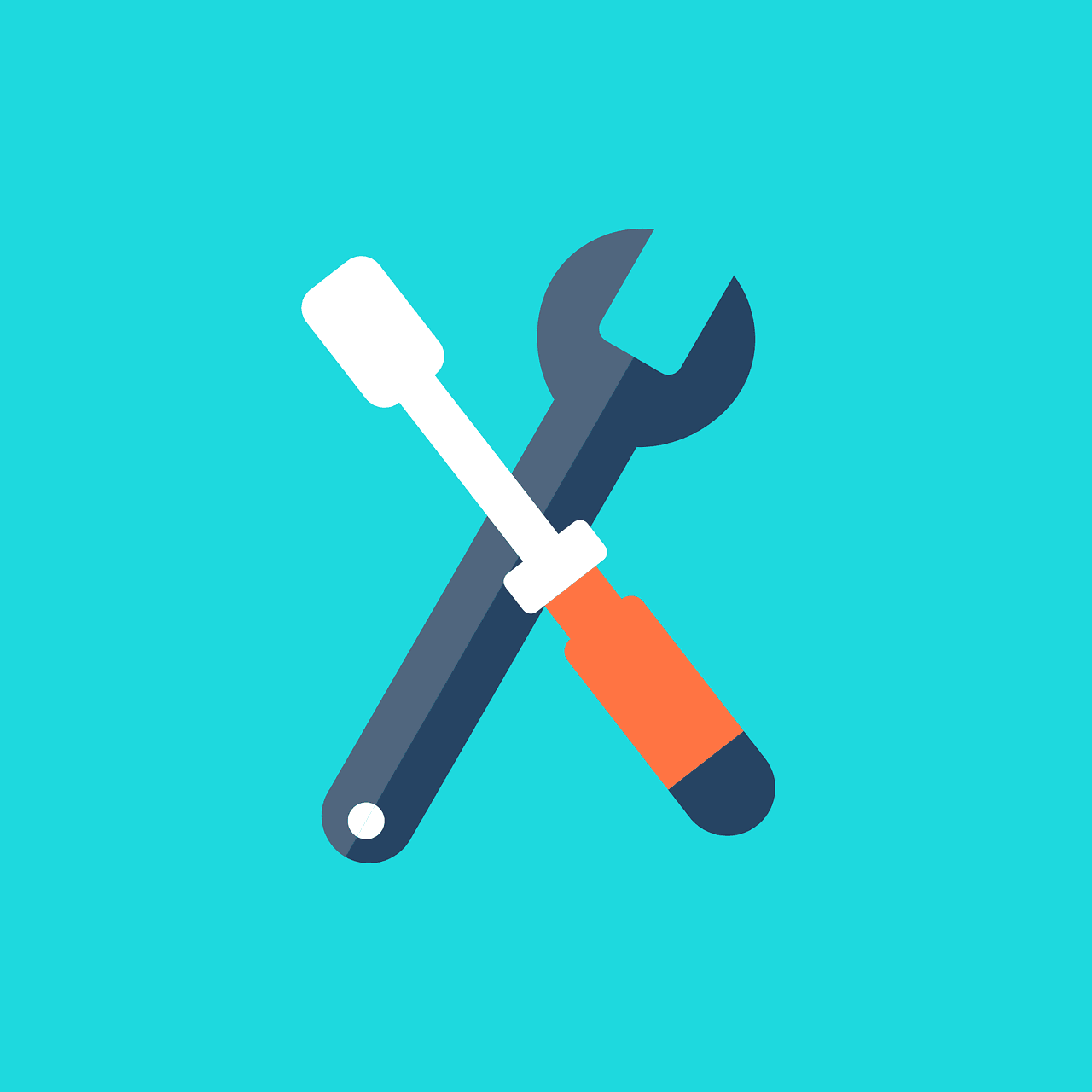
Los sistemas industriales y equipos de cualquier empresa están constantemente expuestos a desgaste, deterioro y fallos inesperados. Cuando una máquina se detiene repentinamente, paraliza la producción y puede generar pérdidas significativas. Es aquí donde entra en juego una estrategia fundamental: el mantenimiento correctivo. Esta práctica, aunque reactiva por naturaleza, constituye un pilar esencial en la gestión de activos industriales. Comprender qué es el mantenimiento correctivo resulta indispensable para cualquier profesional del sector.
Tabla de contenidos
- ¿Qué es el mantenimiento correctivo?
- Características del mantenimiento correctivo
- Tipos de mantenimiento correctivo
- Características del mantenimiento preventivo
- Otros Tipos de mantenimiento preventivo
- Ventajas y desventajas del mantenimiento preventivo
- Ejemplos de mantenimiento preventivo
- Ventajas y desventajas del mantenimiento correctivo
- Ejemplos de mantenimiento correctivo
- Implementación efectiva del mantenimiento correctivo
- ¿Cuándo es apropiado aplicar mantenimiento correctivo?
- La evolución hacia el mantenimiento híbrido
- Preguntas frecuentes sobre qué es el mantenimiento correctivo
- ¿El mantenimiento correctivo es siempre más costoso que el preventivo?
- ¿Se puede combinar el mantenimiento correctivo con otras estrategias?
- ¿Cómo afecta la digitalización al mantenimiento correctivo?
- ¿Existe alguna normativa específica sobre mantenimiento correctivo?
- ¿Qué perfil profesional se requiere para el mantenimiento correctivo?
- ¿Cómo calcular el costo real del mantenimiento correctivo?
- ¿Es posible predecir y presupuestar el mantenimiento correctivo?
- ¿Cuál es la tendencia futura en mantenimiento industrial?
- Conclusión de Qué es el mantenimiento correctivo
- Referencias
¿Qué es el mantenimiento correctivo?
El mantenimiento correctivo es el conjunto de tareas destinadas a corregir los defectos o fallos que se presentan en equipos y maquinarias una vez que estos ya han ocurrido. A diferencia de otras estrategias de mantenimiento, el correctivo actúa como respuesta a una avería o deficiencia funcional que ya está presente, con el objetivo de restaurar la operatividad del sistema en el menor tiempo posible.
Este tipo de mantenimiento se caracteriza por su naturaleza reactiva: se ejecuta después de la identificación de un fallo y busca devolver al equipo a sus condiciones normales de funcionamiento. En esencia, el mantenimiento correctivo responde a la filosofía de «reparar cuando se rompe», un enfoque que, aunque tiene sus limitaciones, resulta inevitable en ciertos contextos industriales.
En términos prácticos, cuando una máquina deja de funcionar correctamente, el equipo de mantenimiento interviene para diagnosticar el problema, reemplazar o reparar los componentes dañados y realizar las pruebas necesarias para asegurar que el sistema vuelve a operar adecuadamente. Esta secuencia de acciones constituye el núcleo del qué es el mantenimiento correctivo.
Características del mantenimiento correctivo
El mantenimiento correctivo posee atributos distintivos que lo diferencian de otras estrategias. Estas características definen su aplicación y determinan su efectividad en diferentes escenarios:
- Naturaleza reactiva: Se implementa como respuesta a un fallo que ya ha ocurrido, no como medida preventiva.
- Inmediatez: Generalmente requiere acción rápida para minimizar tiempos de inactividad.
- No planificado: En su forma más pura, no se programa con antelación, sino que responde a necesidades emergentes.
- Enfoque en la reparación: Su objetivo principal es restaurar la funcionalidad, no prevenir futuros fallos.
- Variabilidad de costos: Los gastos pueden fluctuar considerablemente dependiendo de la gravedad de la avería.
- Personal especializado: Requiere técnicos con capacidad para diagnosticar y resolver problemas diversos.
- Documentación posterior: El registro de las intervenciones suele realizarse después de ejecutar las reparaciones.
Estas características configuran el perfil del mantenimiento correctivo como una estrategia necesaria pero que debe gestionarse adecuadamente para minimizar sus desventajas inherentes.
Tipos de mantenimiento correctivo
Dentro del universo del mantenimiento correctivo, podemos identificar diferentes modalidades según diversos criterios. Esta clasificación nos ayuda a comprender mejor qué es el mantenimiento correctivo en todas sus variantes:
Según su planificación
- Mantenimiento correctivo no planificado: Se ejecuta de forma inmediata tras la aparición del fallo, sin tiempo para planificación. Es la forma más pura de mantenimiento correctivo, respondiendo a emergencias operativas.
- Mantenimiento correctivo planificado: Aunque responde a un fallo ya detectado, permite cierta planificación al no requerir una intervención inmediata. El equipo puede seguir funcionando con el defecto hasta que se programen los recursos necesarios para su reparación.
Según su complejidad
- Mantenimiento correctivo de primer nivel: Incluye reparaciones sencillas que puede realizar el propio operador del equipo, como reajustes simples o sustitución de componentes básicos.
- Mantenimiento correctivo especializado: Requiere personal técnico con formación específica y herramientas especializadas para diagnósticos complejos y reparaciones de mayor envergadura.
Según su alcance
- Mantenimiento correctivo paliativo: Busca resolver temporalmente el problema para mantener el equipo en funcionamiento, aunque sea a capacidad reducida, hasta que pueda realizarse una reparación definitiva.
- Mantenimiento correctivo curativo: Aborda la causa raíz del problema, realizando una reparación definitiva que restaura completamente la funcionalidad del equipo.
Esta diversidad de enfoques permite adaptar las estrategias de mantenimiento correctivo a las necesidades específicas de cada organización y tipo de equipo.
Características del mantenimiento preventivo
Es fundamental distinguir entre el mantenimiento correctivo y el preventivo para implementar una estrategia integral. El mantenimiento preventivo presenta estas características distintivas:
- Naturaleza proactiva: Se realiza antes de que ocurra el fallo, anticipándose a posibles averías.
- Planificación sistemática: Se programa según intervalos predefinidos de tiempo, uso o condición del equipo.
- Reducción de fallos inesperados: Busca minimizar las paradas no programadas mediante inspecciones regulares.
- Prolongación de vida útil: Contribuye a extender la durabilidad de los equipos mediante cuidados periódicos.
- Costos predecibles: Permite presupuestar con mayor precisión los gastos de mantenimiento.
- Documentación previa: Las tareas se definen con antelación en planes y procedimientos detallados.
- Enfoque en la prevención: Su objetivo principal es evitar que ocurran los fallos, no repararlos.
Comprender estas diferencias es esencial para desarrollar un programa de mantenimiento equilibrado que combine adecuadamente ambos enfoques según las necesidades específicas.
Otros Tipos de mantenimiento preventivo
El mantenimiento preventivo, como contraparte del correctivo, también presenta diversas modalidades que conviene conocer:
Mantenimiento preventivo basado en tiempo
Se realiza en intervalos fijos, independientemente del estado del equipo. Incluye actividades como lubricación programada, cambios de filtros o inspecciones periódicas. Por ejemplo, el cambio de aceite de un motor cada 10.000 kilómetros.
Mantenimiento preventivo basado en uso
Se ejecuta según el nivel de utilización del equipo (horas de funcionamiento, ciclos, kilómetros recorridos). Un ejemplo típico es la revisión de una prensa industrial cada 100.000 ciclos de operación.
Mantenimiento predictivo
Aunque técnicamente es una categoría distinta, muchos lo consideran una forma avanzada de mantenimiento preventivo. Se basa en la monitorización constante de parámetros que indican el estado del equipo, permitiendo predecir fallos antes de que ocurran. Utiliza técnicas como análisis de vibraciones, termografía o análisis de aceites.
Mantenimiento preventivo oportunista
Se aprovechan paradas no programadas o tiempos de baja producción para realizar tareas preventivas que estaban planificadas para fechas posteriores, optimizando así los tiempos de inactividad.
Esta diversidad de enfoques preventivos complementa las estrategias correctivas, permitiendo diseñar un programa de mantenimiento integral adaptado a cada contexto industrial.
Ventajas y desventajas del mantenimiento preventivo
Ventajas
- Reducción de paradas imprevistas: Disminuye significativamente las averías inesperadas que interrumpen la producción.
- Mayor fiabilidad: Los equipos operan de manera más consistente y predecible.
- Optimización de la vida útil: Los componentes duran más tiempo gracias al cuidado regular.
- Mejora de la seguridad: Reduce riesgos asociados con fallos críticos de equipos.
- Planificación eficiente de recursos: Permite organizar mejor el personal, herramientas y repuestos necesarios.
- Menor costo a largo plazo: Aunque requiere inversión inicial, suele resultar más económico que enfrentar averías graves.
- Calidad consistente: Contribuye a mantener estándares de calidad en la producción.
Desventajas
- Inversión inicial elevada: Requiere recursos económicos significativos para su implementación.
- Sobremantenimiento: Existe riesgo de realizar más mantenimiento del necesario, generando costos innecesarios.
- Paradas programadas: Requiere detener equipos en funcionamiento para realizar inspecciones.
- Complejidad organizativa: Necesita sistemas de planificación y seguimiento rigurosos.
- Requiere personal especializado: Demanda técnicos formados en técnicas preventivas específicas.
- Posibles fallos inducidos: En ocasiones, la manipulación durante el mantenimiento puede causar nuevos problemas.
- Resultados no inmediatos: Los beneficios económicos suelen manifestarse a medio o largo plazo.
Evaluar estas ventajas y desventajas resulta fundamental para determinar el equilibrio óptimo entre mantenimiento preventivo y correctivo en cada organización.
Ejemplos de mantenimiento preventivo
Para ilustrar mejor qué implica el mantenimiento preventivo en la práctica, consideremos estos ejemplos concretos:
En la industria automotriz
- Cambio periódico de filtros de aire, aceite y combustible
- Revisión y ajuste de sistemas de frenos cada 20.000 km
- Comprobación mensual de presión y desgaste de neumáticos
- Análisis semestral de fluidos hidráulicos en prensas industriales
En instalaciones eléctricas
- Termografía trimestral de cuadros eléctricos para detectar puntos calientes
- Medición anual de resistencia de puesta a tierra
- Revisión semestral de conexiones y aislamiento en líneas de distribución
- Limpieza programada de transformadores cada 5.000 horas de operación
En sistemas informáticos
- Limpieza mensual de componentes internos para eliminar polvo acumulado
- Verificación semanal de sistemas de refrigeración
- Actualización programada de software de seguridad
- Defragmentación trimestral de unidades de almacenamiento
En edificaciones
- Inspección anual de estructuras para detectar deterioros
- Limpieza semestral de sistemas de climatización
- Revisión trimestral de sistemas contra incendios
- Mantenimiento programado de ascensores según normativa vigente
Estos ejemplos demuestran la diversidad de aplicaciones del mantenimiento preventivo a través de diferentes sectores industriales y contextos operativos.
Ventajas y desventajas del mantenimiento correctivo
Ventajas
- Máximo aprovechamiento de la vida útil: Los componentes se utilizan hasta su fallo efectivo.
- Menores costos iniciales: No requiere inversión en sistemas de planificación complejos.
- Simplicidad administrativa: No precisa programación detallada de actividades preventivas.
- Eficiencia en equipos no críticos: Resulta adecuado para sistemas cuyo fallo no genera consecuencias graves.
- Rapidez de implementación: No requiere análisis previos extensos para su aplicación.
- Flexibilidad operativa: Permite mantener operativos los equipos sin paradas programadas.
- Reducción de inventarios: Minimiza la necesidad de almacenar repuestos que podrían no utilizarse.
Desventajas
- Imprevisibilidad: Los fallos ocurren sin aviso, generando interrupciones inesperadas.
- Costos elevados por paradas no programadas: Las interrupciones súbitas suelen resultar más costosas.
- Daños colaterales: Un componente que falla puede dañar otros elementos del sistema.
- Necesidad de personal disponible: Requiere técnicos preparados para actuar ante emergencias.
- Mayor tiempo de inactividad: Las reparaciones no planificadas suelen llevar más tiempo.
- Dificultad para presupuestar: Los gastos son variables e impredecibles.
- Menor vida útil global: El desgaste acelerado reduce la durabilidad total del equipo.
Entender este balance es fundamental para determinar en qué situaciones qué es el mantenimiento correctivo representa la opción más adecuada, a pesar de sus limitaciones inherentes.
Ejemplos de mantenimiento correctivo
Para ilustrar qué es el mantenimiento correctivo en situaciones reales, consideremos estos ejemplos prácticos:
En la industria manufacturera
- Reparación de un motor eléctrico tras su quemado durante la producción
- Sustitución de una bomba hidráulica que ha comenzado a fugar
- Reparación de una cinta transportadora tras la rotura de su banda
- Intervención urgente en un sistema neumático por pérdida súbita de presión
En edificaciones
- Reparación de una tubería que ha reventado y provoca inundación
- Sustitución de sistemas de iluminación que han dejado de funcionar
- Reparación de un ascensor averiado que ha quedado fuera de servicio
- Intervención urgente en un sistema de climatización colapsado en pleno verano
En tecnologías de la información
- Recuperación de un servidor caído por fallo de hardware
- Reparación de redes tras la avería de un switch principal
- Sustitución de discos duros fallidos en sistemas de almacenamiento
- Restauración de sistemas tras ataques informáticos o corrupciones de datos
En transporte
- Reparación de vehículos comerciales averiados durante ruta
- Sustitución de componentes de aeronaves tras detección de fallos
- Reparación de sistemas de frenado en trenes tras incidentes
- Intervención en sistemas de navegación marítima averiados
Estos ejemplos ilustran cómo el mantenimiento correctivo, a pesar de sus limitaciones, sigue siendo indispensable en numerosos contextos industriales y operativos.
Implementación efectiva del mantenimiento correctivo
Aunque el mantenimiento correctivo es reactivo por naturaleza, existen estrategias para optimizar su implementación:
- Protocolos de respuesta rápida: Desarrollar procedimientos estandarizados para diferentes tipos de averías comunes.
- Inventario estratégico: Mantener disponibilidad de repuestos críticos basándose en historiales de fallo.
- Documentación post-intervención: Registrar detalladamente las causas y soluciones aplicadas para crear una base de conocimiento.
- Análisis de causa raíz: Investigar los orígenes de los fallos recurrentes para prevenir su repetición.
- Formación continua: Capacitar al personal técnico en diagnóstico rápido y técnicas de reparación efectivas.
- Herramientas adecuadas: Disponer del equipamiento necesario para intervenciones ágiles y precisas.
- Sistema de priorización: Establecer criterios claros para determinar la urgencia de cada intervención correctiva.
Estas prácticas permiten maximizar la eficacia del mantenimiento correctivo, minimizando sus desventajas inherentes y optimizando los recursos disponibles.
¿Cuándo es apropiado aplicar mantenimiento correctivo?
A pesar de las tendencias actuales hacia estrategias preventivas y predictivas, existen situaciones donde qué es el mantenimiento correctivo resulta la opción más adecuada:
- Equipos no críticos: Sistemas cuyo fallo no paraliza procesos esenciales ni genera riesgos significativos.
- Componentes con patrones de fallo aleatorios: Elementos que no presentan señales detectables de deterioro progresivo.
- Equipos próximos al fin de su vida útil: Activos que serán reemplazados próximamente y no justifican inversión preventiva.
- Costos preventivos desproporcionados: Cuando el costo de prevención supera significativamente el de reparación.
- Equipos redundantes: Sistemas con duplicidad que permiten continuar operando mientras se repara el componente fallido.
- Tecnologías en evolución rápida: Equipos que serán tecnológicamente obsoletos antes de su desgaste físico.
- Limitaciones presupuestarias severas: Organizaciones sin recursos para implementar programas preventivos completos.
Identificar correctamente estas situaciones permite tomar decisiones informadas sobre cuándo el mantenimiento correctivo constituye una estrategia válida y económicamente racional.
La evolución hacia el mantenimiento híbrido
La tendencia actual en gestión de activos industriales apunta hacia enfoques híbridos que combinan estratégicamente diferentes tipos de mantenimiento:
- Análisis de criticidad: Clasificar equipos según su importancia para aplicar estrategias diferenciadas.
- Mantenimiento basado en condición: Monitorizar parámetros clave y actuar solo cuando hay indicios de deterioro.
- Integración con sistemas digitales: Utilizar software especializado para optimizar la gestión del mantenimiento.
- Análisis de datos históricos: Estudiar patrones de fallo para predecir comportamientos futuros.
- Evaluación continua de costos-beneficio: Revisar periódicamente la efectividad de cada estrategia.
- Adaptación a contextos específicos: Personalizar el equilibrio entre mantenimiento correctivo y preventivo según cada industria.
- Capacitación integral: Formar al personal en múltiples enfoques de mantenimiento.
Esta evolución permite superar la dicotomía tradicional entre correctivo y preventivo, adoptando un enfoque más matizado y adaptativo que optimiza recursos y resultados.
Preguntas frecuentes sobre qué es el mantenimiento correctivo
¿El mantenimiento correctivo es siempre más costoso que el preventivo?
No necesariamente. Aunque tradicionalmente se asocia el mantenimiento correctivo con mayores costos, en equipos no críticos o con baja probabilidad de fallo puede resultar más económico que implementar programas preventivos exhaustivos. La clave está en evaluar cada caso específico considerando factores como criticidad, patrón de fallos y costos asociados.
¿Se puede combinar el mantenimiento correctivo con otras estrategias?
Absolutamente. De hecho, la mayoría de las organizaciones implementan estrategias híbridas que combinan diferentes enfoques según la criticidad de cada equipo. Por ejemplo, pueden aplicar mantenimiento predictivo a sistemas críticos, preventivo a equipos importantes y correctivo a componentes secundarios.
¿Cómo afecta la digitalización al mantenimiento correctivo?
La transformación digital ha mejorado significativamente la eficacia del mantenimiento correctivo mediante herramientas como diagnóstico remoto, realidad aumentada para asistencia técnica, sistemas de gestión que optimizan la asignación de recursos y análisis de datos para identificar patrones de fallo recurrentes.
¿Existe alguna normativa específica sobre mantenimiento correctivo?
Aunque no existen normativas exclusivas para mantenimiento correctivo, diversas regulaciones sectoriales establecen requisitos mínimos de mantenimiento en industrias críticas como aviación, energía nuclear o procesamiento de alimentos. Estas normativas suelen enfatizar la necesidad de combinar estrategias preventivas y correctivas.
¿Qué perfil profesional se requiere para el mantenimiento correctivo?
Los técnicos de mantenimiento correctivo deben combinar sólidos conocimientos técnicos con capacidad para diagnóstico rápido y resolución de problemas bajo presión. Requieren formación específica en los sistemas que mantienen, habilidades de análisis y capacidad para documentar adecuadamente sus intervenciones.
¿Cómo calcular el costo real del mantenimiento correctivo?
El costo total debe incluir no solo los gastos directos (repuestos, mano de obra), sino también los indirectos: pérdidas por producción detenida, posibles penalizaciones por incumplimientos, deterioro acelerado del equipo y efectos sobre la calidad del producto. Esta visión integral permite comparaciones válidas con otras estrategias.
¿Es posible predecir y presupuestar el mantenimiento correctivo?
Aunque por definición responde a eventos impredecibles, el análisis estadístico de historiales de fallo permite estimar frecuencias y costos promedios para presupuestar con cierta aproximación. Las técnicas de análisis de datos están mejorando significativamente esta capacidad predictiva.
¿Cuál es la tendencia futura en mantenimiento industrial?
La industria avanza hacia el denominado «Mantenimiento 4.0», que integra Internet de las Cosas (IoT), inteligencia artificial y análisis predictivo para optimizar las estrategias de mantenimiento. Esta evolución no elimina el componente correctivo, sino que lo integra en un sistema más sofisticado y eficiente.
Conclusión de Qué es el mantenimiento correctivo
Qué es el mantenimiento correctivo, lejos de ser una estrategia obsoleta, continúa desempeñando un papel fundamental en la gestión moderna de activos industriales. Su naturaleza reactiva, aunque presenta limitaciones evidentes, resulta inevitable e incluso conveniente en determinados contextos operativos.
La clave para una gestión eficaz del mantenimiento no reside en eliminar completamente las intervenciones correctivas, sino en implementarlas estratégicamente como parte de un enfoque integrado que combine diferentes metodologías según la criticidad y características de cada equipo. Este equilibrio permite optimizar recursos, minimizar tiempos de inactividad y maximizar la rentabilidad global de los activos.
En un entorno industrial cada vez más digitalizado y competitivo, comprender qué es el mantenimiento correctivo, sus fortalezas y limitaciones, resulta esencial para desarrollar estrategias de mantenimiento adaptadas a los desafíos específicos de cada organización. El futuro apunta hacia modelos híbridos, potenciados por tecnologías digitales, que extraigan lo mejor de cada enfoque para crear sistemas de mantenimiento verdaderamente eficientes y adaptables.
Referencias
- Wikipedia: Mantenimiento correctivo
- Asociación Española de Mantenimiento (AEM). (2022). Guía técnica de mantenimiento industrial.
- Instituto Nacional de Tecnología Industrial. (2023). Manual de buenas prácticas en mantenimiento industrial.